No, AAC blocks are grey. Cheeky jokes apart, they aren’t as “green” as they’re purported to be. But why, and how?
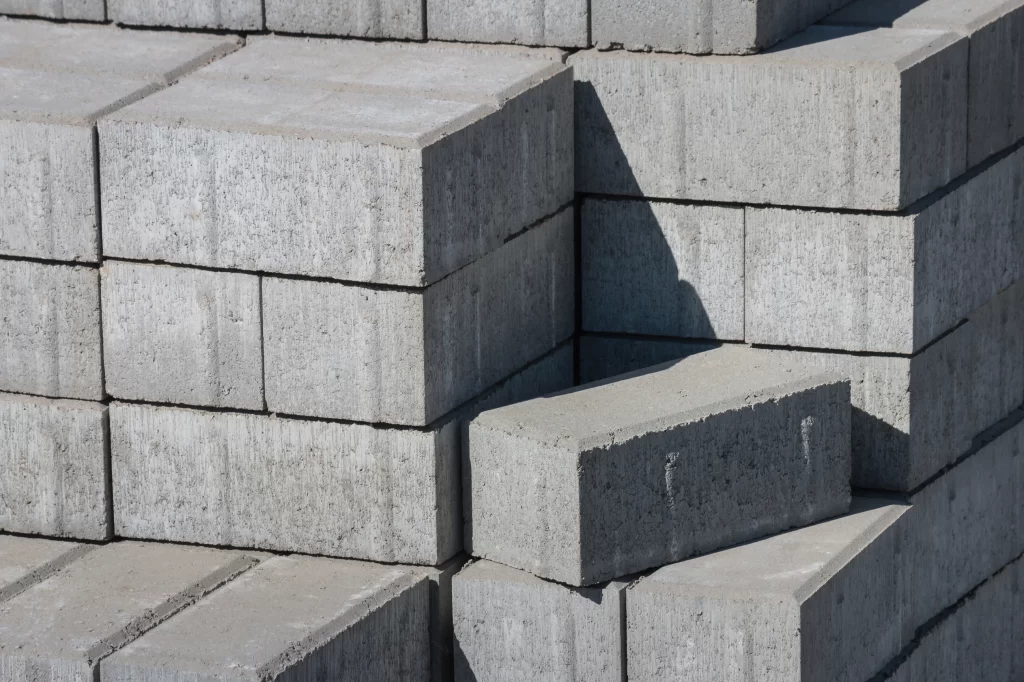
A little background first…
What are AAC Blocks?
Autoclaved Aerated Concrete blocks are made from mixing sand, cement, lime, water and gypsum. They are then cut into pieces and form into cells that are subsequently autoclaved to harden, creating cellular foam blocks. They have a number of features such as being lightweight, having good fire resistance and excellent acoustics; plus they offer thermal insulation, making them an increasingly popular choice for construction projects around the world.
Autoclaved Aerated Concrete (AAC) blocks are the preferred choice of walling material for almost every real estate developer in the market today because they’re cheap and enable faster construction. But they aren’t easy to live with. We’ve learned about the lengths these guys scale to make it all work from our own first-hand encounters with the construction teams at project sites. The blocks are very porous and absorb huge amounts of water; the expansion and contraction are so much that they eventually crack; the plaster de-laminates after a few years of construction; and the structural integrity gets compromised if the chiselling for concealed conduits is not done accurately.
Most importantly (I can’t believe it has actually come down to this), you cannot hammer a nail into the block without shattering it. And to overcome all of these difficulties, builders end up installing RCC tie beams after every 4 rows of the block-work, use only power drills to fix nails, and so on. We have, in fact, heard many complaints about AAC blocks from the QA/QC teams of many major Indian real estate firms like L&T Realty, Shapoorji Pallonji, Mahindra, and so on.
Despite these troubles, most major developers still choose AAC blocks simply because of the lower cost. Adding to the mix, you’d find many manufacturers advertising AAC blocks as a “green” material, and quite a few green-rating systems even award additional points for the use of AAC blocks. Not without merit, though! They have a much higher thermal insulation than clay bricks and are extremely light, reducing the structure’s dead load.
And do you know what’s more astonishing? The embodied carbon of AAC blocks is 0.23 kg.CO2/kg, which is almost as much as the embodied carbon of clay bricks at 0.24 kg.CO2/kg.
But are these benefits enough to call it a “green” material?
Yes and no. You see, it’s about the optics. What is your benchmark? If you’re comparing AAC blocks with red bricks (burnt clay bricks), then they’re much greener. But if you were to compare it with fly ash bricks, not so much. And fly ash bricks in some parts of our country (like Vizag) are almost 98% recycled material, with very low embodied energy because of the nature of the manufacturing process. And that brings us to the elephant in the room – the manufacturing process of AAC blocks.
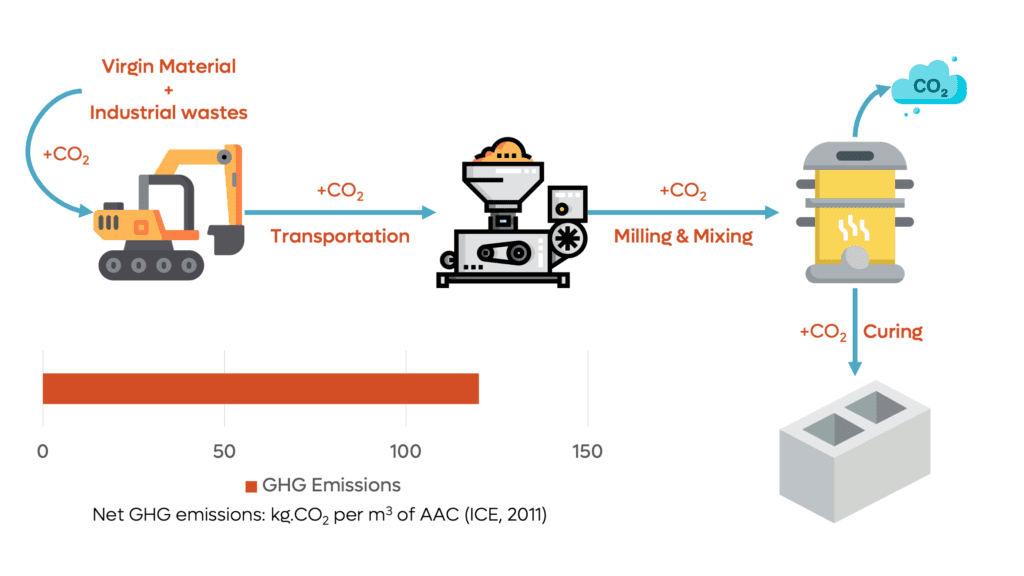
An oversimplified AAC blocks manufacturing process illustration
In a nutshell, the manufacturing process is extremely complex, with numerous steps and infinite moving parts. Obviously, it is fungible. The illustration above is an oversimplified manufacturing process infographic. Without going into extreme specifics here, I have outlined the various steps involved in the manufacturing process, along with the associated embodied carbon values in the image below.
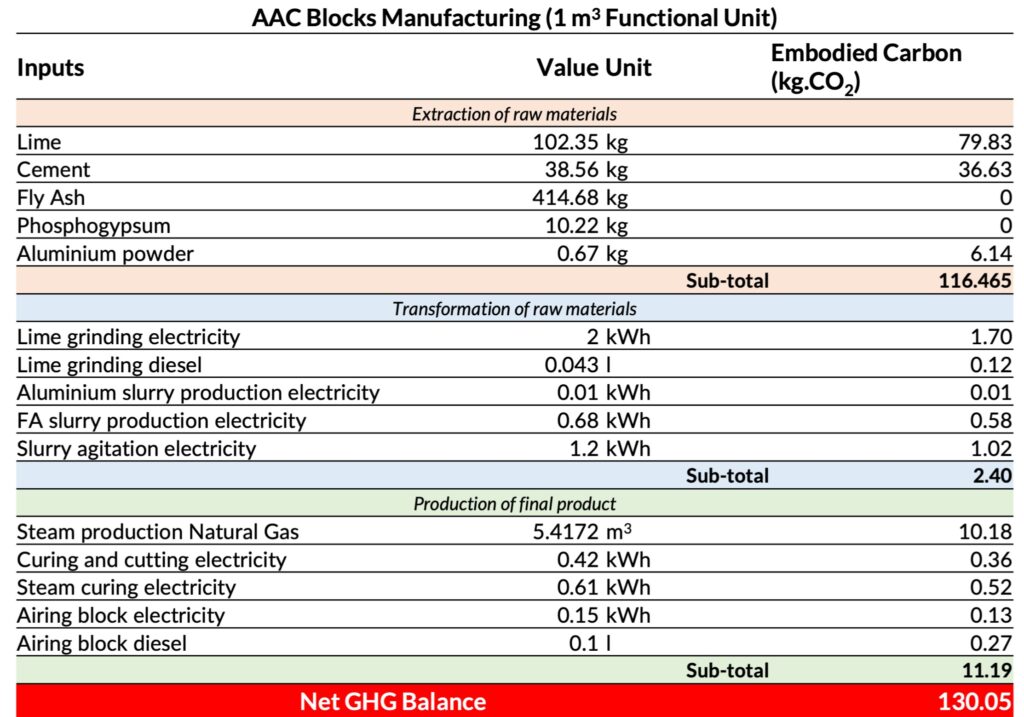
The item-wise embodied carbon calculations of 1 cubic metre of AAC blocks
To sum it up, each cubic metre of AAC blocks manufacturing emits about 130 kg of carbon dioxide. A typical 1000 sq ft apartment requires about 40 – 45 cubic metres of AAC blocks, which means that the walls alone would be responsible for 5.2 –5.9 tonnes of carbon dioxide emissions. You would emit as many carbon dioxide emissions if you drove your car a distance of more than 45,000 km!
And do you know what’s more astonishing? The embodied carbon (which is expressed as a ratio of the mass of carbon dioxide emissions to the mass of the material) of AAC blocks is 0.23 kg.CO2/kg, which is almost as much as the embodied carbon of burnt clay bricks (the most environmentally harmful walling material) at 0.24 kg.CO2/kg. In practice, however, the carbon emissions coming from walls made of AAC blocks would definitely be lower than burnt clay brick walls because of the lighter weight of the material.
But doesn’t it make you stop and wonder if AAC blocks are “green” enough?
Parting words…
For many people, AAC blocks are at the pinnacle of green construction. And reading through this blog might have been a little uncomfortable. If we were to survive the climate change pandemic, the first step would be to educate ourselves about the perils of the convention. I hope that this blog becomes a first step at doing that for many. Embodied carbon is seldom spoken about in the construction industry. But I’m confident that it shall catch on, just like embodied energy did for the past few decades. Except, we do not have a few decades and we need to start speaking about embodied carbon posthaste.
Also, it doesn’t make sense to speak about a problem without offering solutions. And we have it in the form of Agrocrete®. More about its advantages over AAC blocks and other materials in the next blog!